Several requirements in the production of precision casting equipment
- Share
- Issue Time
- May 9,2020
Summary
Several requirements in the production of precision casting equipment
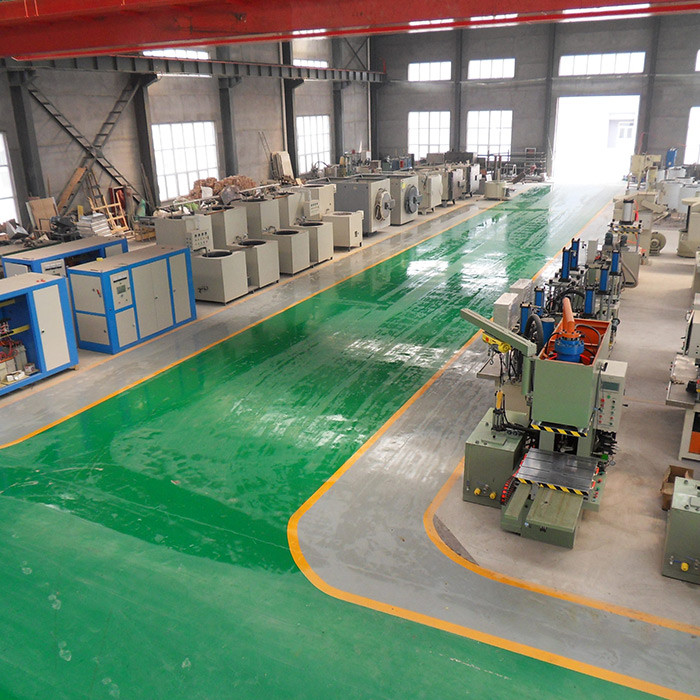
Several requirements in the production of precision casting equipment
We need to use precision casting technology in the production of precision casting equipment, so what are the technical requirements in production? Today I will introduce to you some requirements in the production of precision casting equipment.
Method adaptation
For example, sand casting, mass production factories should create conditions to adopt technologically advanced modeling and core making methods. The production line of the old-style shock-type or shock-pressure molding machine is not high in productivity, the labor intensity of the workers is large, and the noise is large. It cannot adapt to the requirements of mass production and should be gradually reformed. For small castings, you can use a horizontal or vertical parting boxless high-pressure molding machine production line, the real molding production is high in efficiency, and the area is small; for middle parts, you can use a variety of boxed high-pressure molding machine production lines, gas The molding line is punched to meet the requirements of a fast and high-precision molding production line. The core making method can be selected: cold core box, hot core box, shell core and other efficient core making methods.
For medium-sized large-scale castings, resin self-hardening sand molding and core making can be considered.
For single-piece, small-batch production of heavy castings, manual molding is still an important method. Manual molding can adapt to various complex requirements and is relatively flexible, without requiring a lot of process equipment. Water glass sand type, VRH method water glass sand type, organic ester water glass self-hardening sand type, clay dry type, resin self-hardening sand type and cement sand type, etc .; for single-piece heavy castings, the pit molding method is low in cost and put into production fast. It is more appropriate to use multi-box molding and split-box molding for mass-produced or long-term stereotyped products. Although molds, sand boxes, etc. start to invest heavily, they can be compensated for saving molding time and improving product quality.
Low-pressure casting, die casting, centrifugal casting and other casting methods are only suitable for mass production because of the high cost of equipment and molds.
Conditional methods should be suitable
For example, it is also used to produce castings such as large machine tool beds. The core forming method is generally used, and the core is formed in the pit without making patterns and sand boxes; while other factories use the sand box molding method to make patterns. Different enterprise production conditions (including equipment, venues, staff quality, etc.), production habits, and accumulated experience are different. Based on these conditions, what products are suitable and what are not (or cannot) products should be considered.
Precision requirements and costs
The precision of castings obtained by various casting methods is different, the initial investment and productivity are also inconsistent, and the final economic benefits are also different. Therefore, to achieve more, faster, better, and more economical, all aspects should be taken into consideration. A preliminary cost estimate should be made of the casting method selected to determine the casting method with high economic benefits and which can guarantee the casting requirements.
Although the development of China's foundry industry is in a relatively difficult period, from a long-term perspective, there is still some hope for the development of China's precision casting industry, the market demand has slowly begun to pick up, and plus China's casting industry With the development of the strong strength, I believe that China's foundry industry will achieve gratifying results.
Experts said that in order to fundamentally improve the level of casting technology, the following four points must be achieved: First, develop simulation technology, improve the accuracy of prediction, strengthen process control, and improve the yield. The problem of regularity is not well grasped, which affects the yield in mass production. Second, the combination of production, education and research. In addition to the enhancement of innovation awareness and R & D capability, the independent innovation of enterprises also needs to pay attention to and strengthen the combination of “production, learning and research” with precision casting enterprises as the main body. Third, pay attention to material research and development. Materials are the foundation of industry, and there is still much work to be done. In the aerospace field, the research and smelting technology of some new materials such as alloy materials, especially high-temperature alloys, need to be improved, and the gap with foreign countries is still relatively large. Fourth, pay attention to the improvement of equipment technology. The process is still mainly a problem of equipment. Many key equipment, such as some directional solidification equipment, mainly rely on imports, so the research and development of precision casting equipment is still the focus.