What Is the Continuous Casting Process?
- Share
- Issue Time
- Jun 8,2022
Summary
Continuous Casting Process Explained | Types Of Continuous Casting
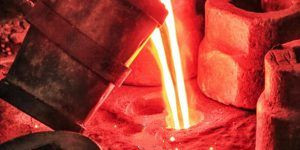
Continuous casting is a manufacturing process that allows metals and metal alloys to be shaped then solidified without interruption. Metal is poured into a mold and rapidly chilled to ensure a uniform grain structure within the metal. Most often, these shapes are tubes and solids, but can also include squares, rectangles, and other irregular shapes as requested. This method improves quality and is more cost-efficient than other options, such as sand casting.
Continuous casting of steel was first introduced in the 1950s as an alternative method of steel manufacturing. It is now a standard manufacturing method. Here’s how the process works.
Overview of the Continuous Casting Process
The continuous casting process allows a metal or metal alloy to be partially shaped, cooled, and then stretched before it is finally solidified into the shape it is meant to be, often using a sand casting machine. Here is the process:
- Molten metal is ladled or fed into a mold of the shape required.
- Heat is extracted from the metal by placing cooled water around the mold. The metal is given its basic shape (from the mold) and is partially solidified.
- Semi-solid metal is then sent through a guide that will stretch the material to a thickness desired by the customer. The metal continues cooling in this stage.
- Fully solidified metal is sent through straighteners to achieve the final dimensions.
- The metal product is withdrawn and cut to the needed length by saws.
Continuous casting can be done vertically or horizontally. The vertical method is the most common, but the horizontal method is starting to gain traction. The process using either method is the same, but the layout of the equipment is different. In the vertical method, the equipment is “stacked” upright and contained on more than one floor of your building. With the horizontal method, the equipment is stretched out all on one level.
Advantages of Continuous Casting
Continuous casting has many advantages. For starters, with other casting methods, it is difficult to cast metal into long, tubular forms. With continuous casting, you can make long tubes in a variety of shapes and sizes. Here are some of the other advantages to consider:
- Continuous castings are perfect for pressure applications. They are consistently homogeneous and dense.
- Less machining stock is needed.
- Less material is wasted than some other casting methods.
- These castings are straight and concentric, meaning there is no deviation. You get the same product every time.
- Suppliers often maintain stock of standard products, available to distributors on demand.
- Cost advantages can be offered for standard shapes and sizes.
Disadvantages of Continuous Casting
There are a few limitations to consider when looking at continuous casting. The biggest is the cost of setup. Due to both the high cost of creating a mold and the time spent setting up the machine for each project, it is not practical to use this method for small quantities or for special shapes of a product. It also isn’t economical to use this method with special metal alloys in smaller quantities.
Another thing to consider is the shapes that can be cast. Continuous casting is limited to more simple shapes that have a stable cross-section. This method is not a good option for some of the more tedious, difficult casting projects.
A Solid Casting Solution
Continuous casting is a cost-effective way to produce basic metal shapes and tubes out of almost any metal or metal alloy. Products that are cast this way are homogenous and of considerable quality. Because of the way these products are made, distributors and other customers know they are getting a consistent product every time. With very little waste material, the process is also eco-friendly.
OBT has always been a trusted partner in the foundry industry. We provide precision casting, die casting, sand casting, lost wax casting, forging and other processes. Surface treatment methods include sandblasting, chrome plating, dipping, hot dipping, surface hardening, powder coating, galvanizing, etc. Mainly used for auto parts, marine hardware accessories, railway transportation accessories, furniture hardware, machined parts and pump valves.