The Advantages of Gravity Die Casting
- Share
- Issue Time
- Jun 10,2022
Summary
OBT has always been a trusted partner in the foundry industry. We provide precision casting, die casting, sand casting, lost wax casting, forging and other processes.
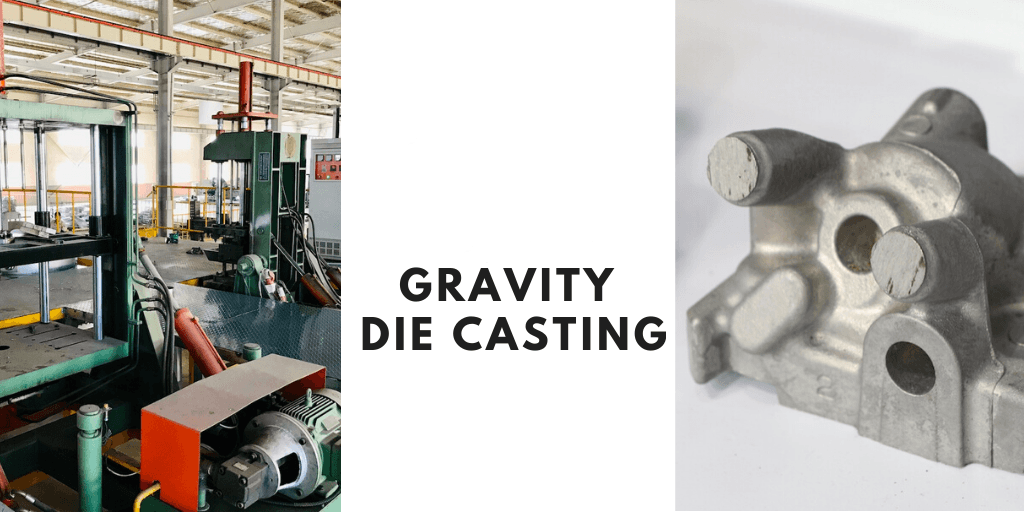
Gravity die casting is used to fabricate metal alloys with dense, high-quality mechanical attributes. Sometimes called permanent mold casting, the process involves pouring molten metal into molds using a ladle and – as the name would suggest – relying on gravity alone to fill them. Other die casting processes require the use of gasses or vacuums to create enough pressure on the alloy to settle into all channels within the mold. The gravity method results in several advantages, including smoother surfaces, exceptional dimensional accuracy, and faster production times.
Gravity casting also tends to be more cost-effective than other processes, as it does not require any large or complex machinery to inject the metal into the molds. Additionally, the molds themselves are reused indefinitely, thereby reducing wasted time and resources needed to constantly produce new dies. This method produces high volume, quality casts that require very little finishing.
Gravity Die Casting: Materials & Process
Typically, this method works best with non-ferrous alloys like zinc, copper, and aluminum. It is usually done manually but can also be automated in certain circumstances. The process is a simple one: first, the mold goes through heat treatment and is then coated with a lubricating die release agent, which allows easy removal of the cast after it has cooled. Then, the liquid metal is poured into the cavity and allowed to flow into every dimension of the mold. Sometimes, a tilting technology is applied to direct the flow of metal into more complex recesses within the die. After it has cooled and solidified, the cast is removed and refined to remove any sharp edges or extra material.
Automotive Industry & Gravity Die Casting
Manufacturers typically invest in well-designed, significantly tooled permanent molds, which results in valuable consistency in the finished products. Surface details are reliably reproduced due to the long-term reusability of the molds, which are generally formed using durable materials like grey cast iron, graphite, and stainless steel. Although gravity casting works best for simply shaped, single-part molds, it can also produce more complex casts effectively. Gravity casting is widely used in virtually every sector of the modern world, with a strong presence in the automotive industry. From cylinder heads to engine support, many light-alloy automotive components are created with gravity die casting.
Alternatives to Gravity Die Casting
Aluminum die casting is often used for larger production orders rather than gravity die casting. Sand casting is used to create three-dimensional hollows and more complex molds than those used in gravity die casting, but it usually has higher tooling costs.
Investment casting is another viable alternative to gravity casting if a high production run is necessary. The high-pressure automated filling process reduces errors and the need for secondary machining but can be more expensive to set up.
OBT has always been a trusted partner in the foundry industry. We provide precision casting, die casting, sand casting, lost wax casting, forging and other processes. Surface treatment methods include sandblasting, chrome plating, dipping, hot dipping, surface hardening, powder coating, galvanizing, etc. Mainly used for auto parts, marine hardware accessories, railway transportation accessories, furniture hardware, machined parts and pump valves.