Casting Production Costs & Processes: A Guide for Metal Castings
- Share
- Issue Time
- Jun 13,2022
Summary
There isn’t a one-size-fits-all approach in identifying the processes and casting production costs for your project. And ultimately, it depends largely on what type metal is used.
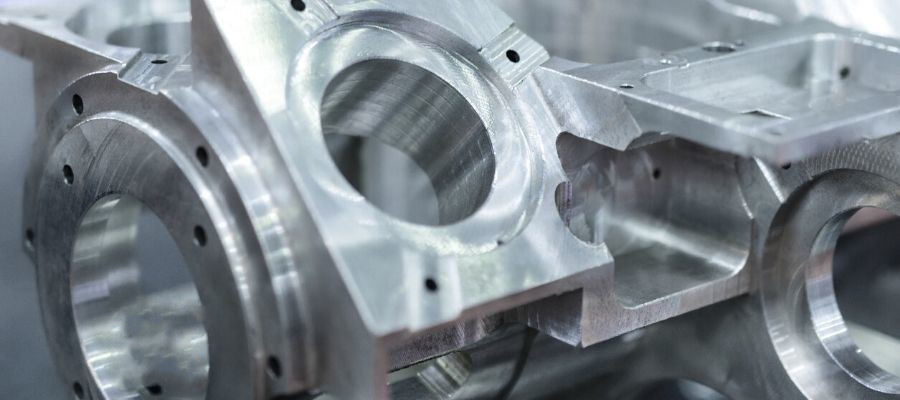
There isn’t a one-size-fits-all approach in identifying the processes and casting production costs for your project. Aside from the amount of metal required, the total cost and processes depend on a multitude of other factors, including design complexity, cast surface finish, dimensional allowances and tolerances, quality levels, and quantity of products. And ultimately, it depends largely on what type metal is used.
First, it’s important to know the market prices of the metals you’ll be using and supply chain conditions. We recommend using Fastmarkets AMM metal price tracker. While current pricing is the most important figure, pricing trends and supply chain information will give you the foresight to order additional inventory if price increases are expected in the near future.
Carbon Steel Casting
One popular material for investment casting is carbon steel. Carbon steel has a lower cost than stainless steel, but it’s important to distinguish between low carbon and high carbon steel. High carbon steel is popular for kitchen utensils and tools; it’s very hard and retains its shape. Low carbon steel has the lowest production costs and it’s easy to use in manufacturing processes. Low carbon steel can be found in bolts, panels, plates, and tubes. Process options in carbon steel casting include sand casting, centrifugal casting, and permanent mold casting.
Alloy Steel Casting
Alloy steel is usually less expensive than stainless steel casting, and it’s perfect for projects that require machinability and corrosion resistance. Due to its corrosion resistance, it’s often used in appliances, pipes, and energy applications. The steps involved in the process of alloy steel casting are pattern production, mold making and preparation, wax model/tree assembly, sand shell & dewaxing, material pouring, refining, and testing. Because alloy steels resist wear and corrosion, they’re also good for industrial and commercial applications which require higher strength.
Aluminum Investment Casting
Popular in the aerospace, automotive, and machine industry, aluminum investment casting offers accuracy in the production of many complex and lightweight components. The process of aluminum casting involves pattern production for mold preparation and injection of a wax into the mold. The mold is then sanded and de-waxed. The casting is polished, then tested and machined. Aluminum cast products are hailed for their full recyclability, thermal conductivity, and the ability to withstand high operating temperatures. When compared to stainless steel, aluminum is usually more expensive than stainless steel. There are a few exceptions, but the raw material price of aluminum is usually high enough to drive prices up.
Copper Casting
Like aluminum casting, copper casting is also used in the production of complex parts. Several copper and copper-based casting materials exist, including brass, bronze, and beryllium copper. Process options in copper casting are sand casting, centrifugal casting, and permanent mold casting. Not only does copper casting offer design flexibility, a superior surface finish, and tight tolerances; costly machining operations may also be avoided.
Gravity Die Casting
Gravity casting is a form of die casting, usually deployed in conjunction with non-ferrous alloys such as copper, zinc, and aluminum. The gravity die casting process results in ultra-strong, ultra-durable alloy fabrications that are ideal for heavy-duty use. Our customers then deploy these components and equipment pieces in high-pressure, high-strain environments, where they perform with aplomb.
Stainless Steel Casting
Stainless steel casting can be employed for specialized projects in the industries of aircraft, medical equipment, construction, railway, industrial, and automotive. This casting can be done with the use of stainless steel types that contain chromium, nickel, low carbon stainless, and molybdenum. Melting, casting, forming (hot rolling), heat treatment, descaling, cutting, finishing, hardening, and testing are the processes in stainless steel casting.
Cost Estimates
Once it’s been determined what metal type and processes are best for a particular desired outcome, material costs can be estimated, and so can labor cost, setup, tooling, energy, and finishing costs. Still, investment casting cost estimates are specific and unique to every project, so once you’ve gathered all the information you can and outlined the factors for your project, it’s important to seek out a consultation with an expert casting team. Working with a reputable casting foundry from the start will help to ensure that your estimates are reliable, not only in the sense of cost, but lead time as well. If you choose a foundry based solely on price, a late start or delivery could end up costing you more in the long run.
OBT has always been a trusted partner in the foundry industry. We provide precision casting, die casting, sand casting, lost wax casting, forging and other processes. Surface treatment methods include sandblasting, chrome plating, dipping, hot dipping, surface hardening, powder coating, galvanizing, etc. Mainly used for auto parts, marine hardware accessories, railway transportation accessories, furniture hardware, machined parts and pump valves.