Investment Casting Process
- Share
- Issue Time
- Jun 14,2022
Summary
Investment casting is one of the most widely used processes in metal casting, especially for parts within the transportation and equipment industry.
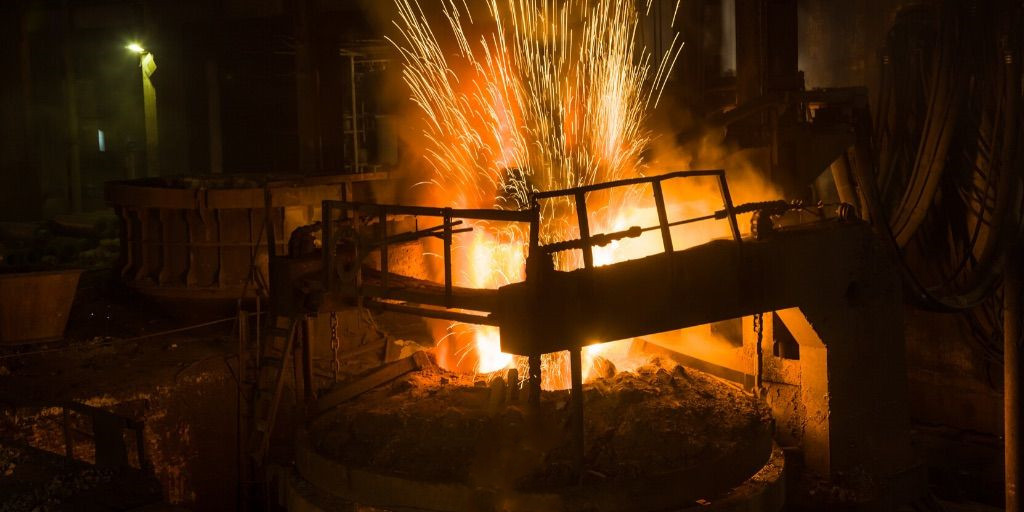
Investment casting is one of the most widely used processes in metal casting, especially for parts within the transportation and equipment industry. Prized for its strength, hardness, and resistance to corrosion, steel is the most common material used for investment casting, but other metals are also utilized in the investment casting process.
The end of the casting process does not necessarily mean the product or component is market-ready. Heat treatments and precision machining are often part of the process. Depending on its final use and purpose, the final casts may undergo extensive treatment and testing after the initial casting.
By heating and cooling the cast metal at different rates, the mechanical properties of the metal can be modified to meet the standards for a product in any industry. When researching the investment casting process, keep this checklist in mind when choosing the right casting foundry:
Mold Making
Molds are the foundation of investment casting. Through mold making, the molten metal is poured into a mold and re-form into the perfect pattern of the part. This process provides tolerances within thousandths of an inch, providing the precision required to make wear-resistant parts with complex geometries.
Investment Casting Process for Metal Components
Investment casting produces strong, reliable metal parts and components.
Normalizing metal is a similar process to annealing, but in this case, the cast is removed from the furnace and allowed to cool in the atmosphere. The irregular cooling pattern that normalizing produces generally creates a finished metal that is stronger and harder than annealed metal.
Materials for Investment Casting
The investment casting process uses for a variety of metals:
- alloy steel
- aluminum
- carbon steel
- copper steel
- stainless steel
The most common material used for investment casting is stainless steel. Stainless steel casting is used for the freight and transportation industries, aviation, hardware and tool industry, electrical, and the arms industry. Stainless steel is popular for several reasons; a long service life and lower maintenance costs make it the the choice for over 70% of production runs.
Does Investment Casting Reduce Lead Times and Cut Costs?
Yes! The modern investment casting process is mechanized and it’s been perfected over decades of industrialization. By mass producing precise, accurate units with tight tolerances, weight and lead times can be achieved with the best cost-per-part scenario.
Investment Casting Costs
Pricing will vary by industry, but at OBTcastings, we deliver accurate investment casting cost estimates that will ensure time and money savings from the start. For material cost estimation, the foundry that you choose will estimate the amount of material required, the finishing process, and shipping. Metal prices are determined by the market, but an experienced foundry will have the most up-to-date pricing available.
OBT has always been a trusted partner in the foundry industry. We provide precision casting, die casting, sand casting, lost wax casting, forging and other processes. Surface treatment methods include sandblasting, chrome plating, dipping, hot dipping, surface hardening, powder coating, galvanizing, etc. Mainly used for auto parts, marine hardware accessories, railway transportation accessories, furniture hardware, machined parts and pump valves.