What are the problems in processing titanium alloys?
- Share
- Issue Time
- Apr 6,2023
Summary
What are the problems in processing titanium alloys?
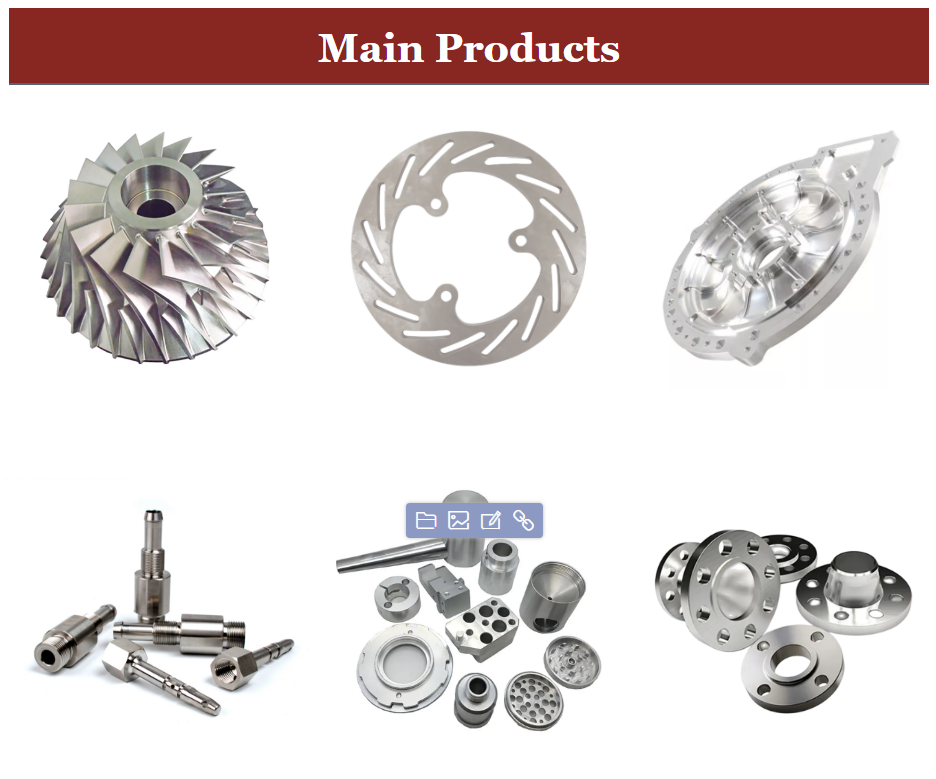
What are the problems in processing titanium alloys?
Volume stamping, free forging and other operations related to processing large cross-section and large-size blanks are carried out in a heated state (≥yS transformation temperature). The heating temperature range of forging and stamping is between 850-1150℃. Alloys BT; M)0, BT1-0, 0T4~0 and T4-1 have satisfactory plastic deformation in the cooling state. Therefore, most of the parts made of these alloys are stamped without heating after intermediate annealing. When Chin alloy is cold plastically deformed, regardless of its chemical composition and mechanical properties, its strength will be greatly improved, and its plasticity will be correspondingly reduced. Therefore, annealing treatment between processes must be carried out.
The blade groove wear seen in bowl alloy processing is the local wear of the back and front along the depth of cut direction, which is often caused by the hardened layer left by the previous processing. The chemical reaction and diffusion between the tool and the workpiece material at a processing temperature exceeding 800°C is also one of the reasons for the formation of groove wear. Because during the machining process, the particles of the workpiece accumulate in the front of the blade, and are "hardened" to the blade under high pressure and high temperature, forming built-up edge. When the built-up edge peels away from the cutting edge, it takes the carbide coating of the blade with it.
Due to titanium's heat resistance, cooling is critical during machining, the purpose of which is to keep the edge and surface of the tool from overheating. Use end coolant for optimum chip evacuation when shoulder milling as well as face milling pockets, pockets or full slots. When cutting titanium, chips can easily stick to the cutting edge, causing the next round of milling cutter rotation to cut chips again, often causing edge line chipping. Each insert cavity has its own coolant hole/injection to solve this problem and enhance constant edge performance. Another clever solution is threaded cooling holes. Long edge milling cutters have many inserts. Applying coolant to each hole requires high pump capacity and pressure. But it is different, it can block the unnecessary holes according to the needs, so as to maximize the liquid flow to the holes in need.